By: Scott Lance, CCP, EBCP, LEED AP O+M, Regional Director
As winter wraps up in the Northeast region of the United States, it’s time to begin thinking about entering back into the cooling season.
A lot of facilities shut down their cooling operations during the winter months; this includes items such as draining down cooling towers and exterior condenser water piping, shutting down chilled water and condenser water pumps for the winter season, and stopping chemical treatments of these systems. Now is the time to start performing some operational checks before that first warm day happens.
The simplest task to do while your chilled water systems are shut down, is to start-up pumps and recirculate water through the entire interior chilled water system. This will break-up any rust scale that may have settled in the system throughout the winter and collect this material in wye strainers and suction screens of pumps. Once the recirculation has occurred, clean out the strainers and screens. During the recirculation operation, check motor voltage and amperage for all three phases of power; this will help determine if the pump motor has any issues. You’ll notice it in the amperage readings, or it will determine if there is a phase imbalance issue with the incoming power.
Also, look for leaks while the system is running; when pumps sit for an extended period and then start back up, it may cause a shaft seal to leak. Identifying a leak now and repairing it will be more convenient than when chilled water is required to be online and stable.
This is also a great time to check the calibration of the sensors. Since the main cooling source will be offline, the supply and return sensors for primary and secondary circuits should be closed regarding measuring water temperature, if the air handling unit coils are piped three-way. If the system is piped two-way, remove thermostats from wells and insert an electronic calibrated device to check temperature. Flow meters can be confirmed using an HDM, pressure gauges at the pump, electrical readings and the pump curves. Certain kinds of flow meters drop calibration when they sit for extended periods of time without water flow. While the system is shut down, look at the pressure gauges and sensors. Inlet and discharge sensors for pumps should read the same value when the pump is offline; if the values are off, then there is a gauge issue. Gauges are great for operational checks while a system is running, but if they are not accurate, then your check is not legitimate.
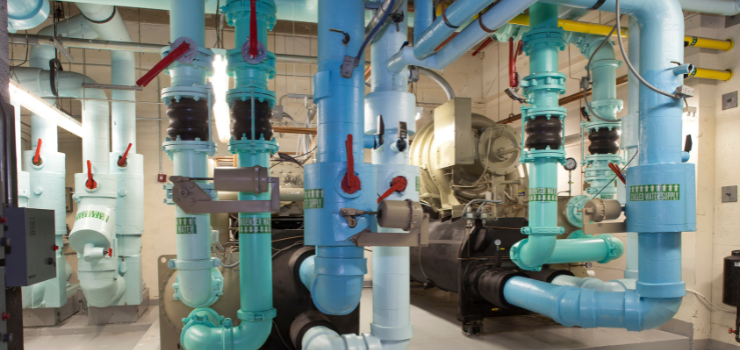
Look at your chillers; look for leaks, water, and oil. Test the refrigerant purge system, if one is present, while the system is shut down. Remember, lots of these systems use a vacuum pump and have been pulling back dust all winter while the system is down. You’ll more than likely have a refrigerant leak when the chiller comes online because it has been sitting non-operational for an extended period. This is also the last chance to check tubes for leaks, so verify the refrigerant charge throughout the winter.
Cooling towers have been offline and drained for the winter. Just because they are empty doesn’t mean they are good to go. Birds might have made a stop-by for a while; dust collects in the basin and media and snow and ice melt might be adding some water to the basin, which could have cracked tower media or wreaked havoc on the tower fan motors. Bump, start the fans and take electrical readings, check that the fan blades are balanced and perform a physical inspection of the entire tower.
The other issue is that the condenser water system might have been sitting dry all winter. The inside of the piping rusts slower when water is present and oxygen is low. But when the water is gone and air is in the piping, it will start to scale. Look at the weather forecast, and toward the end of the season, when it’s still too cold to run but not cold enough to freeze, give that system a good flush and clean the strainers afterwards.
Another item that gets overlooked is conductivity sensors; these are designed to always be submerged, detecting water conductivity; they don’t like going dry. Make sure these sensors still read accurately to ensure that system blow downs or chemical additions are properly calculated by the water condition controls system. This will save money on chemicals or when buying municipal water for make-up after a blow down has occurred.
Many of these checks are very minimal and will take nominal time when the system is not required to be online full time. Identifying issues now will cost less to correct and lessen general aggravation, as opposed to finding them when the cooling season is in full swing.
Questions on how to bring your building back in shape? Contact us at info@fsttechnical.com